Steel Alloy 53 View AMS Numbers >
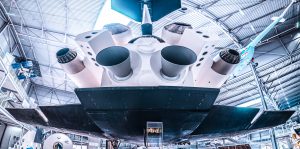
Steel Alloy 53
Steel Alloy 53 is carburizing steel used in power transmission components, such as gears, drive shafts and fasteners. The best example for the use of Steel Alloy 53 is in the aerospace industry. This steel also has high case hot hardness, high surface hardness, abrasion resistance, and outstanding resistance to tempering. Thanks to this, gears and drive shafts made of Alloy 53 can be used in severe conditions, such as high temperatures and low levels of lubrication. Despite the excellent surface hardness, Alloy 53 has a flexible core, which makes it an excellent choice for transferring large impact loads.
Tech Steel & Materials offers Steel Alloy 53 in 1-subtype specification and two shapes/forms:
- AMS 6308 (Bar and Forging)
Chemical Composition
Element | min % | max % |
Carbon, C | — | 0.1 |
Silicon, Si | — | 1 |
Chromium, Cr | — | 1 |
Molybdenum, Mo | — | 3.25 |
Manganese, Mn | — | 0.35 |
Vanadium, V | — | 0.1 |
Nickel, Ni | — | 2 |
Copper, Cu | — | 2 |
Iron, Fe | *Balance |
*Not exclusively to the element mentioned, but that one predominates other elements that are used only in minimal quantities.
Heat Treatment
Several different carburizing heat treatments for Steel Alloy 53 are proposed, all of which give different properties to the alloy. For use in gears and drive shafts, low pressure carburizing might be the preferred method because it provides the part with an outstanding surface hardness and impact strength. This method requires the use of a vacuum furnace and sub-zero treatment in a cryogenic chamber. The precise list of steps is as follows:
- Carburizing is done at the temperature range of 1600 – 1700°F (870 – 930°C) in a vacuum furnace.
- Then the part should be slowly cooled down, followed by annealing for removing the internal stresses. Chill until the alloy reaches room temperature.
- Oil- or high-pressure nitrogen quenching is then done at 1660 – 1700°F (905 – 920°C).
- Sub-zero treatment at temperatures below -100°F (-75°C) ensures that the hardened layer exceeds the hardness of 60 HRC.
- Tempering is done at 300 – 550°F (150 – 290°C) for the strength of approximately 1200 MPa and impact resistance in the region of 100 – 150 J.
Mechanical Properties
Imperial | Metric | |
Hardness, Brinell (Estimated from Rockwell C for 3000 kg load, 10 mm ball Brinell measurement) |
334 | 334 |
Hardness, Knoop | 363 | 363 |
Hardness, Rockwell C | 36 | 349 |
Hardness, Vickers | 349 | 349 |
Tensile Strength, Ultimate | 170000 psi | 1172 MPa |
175100 psi @ 351°F | 1207 MPa @ 177°C | |
193000 psi @ -65.2°F | 1331 MPa @ -54°C | |
Tensile Strength, Yield | 140000 psi (offset not given) | 965 MPa (offset not given) |
130000 psi @ 351°F (offset not given) | 896 MPa @ 177°C (offset not given) | |
160000 psi @ -65.2°F (offset not given) | 1103 MPa @ -54°C (offset not given) | |
Elongation at Break | 16% | 16% |
12% @ 351°F | 12% @ 177°C | |
18% @ -65.2°F | 18% @ -54°C | |
Reduction of Area | 66.5% | 66.5% |
46% @ 351°F | 46% @ 177°C | |
63% @ -65.2°F | 63% @ -54°C | |
Fracture Toughness | 118 ksi-in½ | 130 MPa-m½ |
Charpy Impact | 95.9 ft-lb (V-notch) | 130 J (V-notch) |
114 ft-lb @ 351°F (V-notch) | 155 J @ 177°C (V-notch) | |
40.6 ft-lb @ -65.2°F (V-notch) | 55.0 J @ -54°C (V-notch) | |
Thermal Properties |
||
CTE, linear | 6.256 µin/in-°F @ 75.2 – 199°F | 11.26 µm/m-°C @ 24 – 93°C |
6.700 µin/in-°F @ 75.2 – 500°F | 12.06 µm/m-°C @ 24 – 260°C | |
7.250 µin/in-°F @ 75.2 – 1000°F | 13.05 µm/m-°C @ 24 – 538°C | |
Physical Properties |
||
Density | 0.282 lb/in³ | 7.80 g/cc |
Select AMS Number:
AMS Number | Alloy | Type | UNS | Cross Ref. Spec | Misc./Shape | |
---|---|---|---|---|---|---|
AMS 6308 Bar | Alloy 53 | Steel | K71040 | - | Bar |
![]() |
AMS 6308 Forging | Alloy 53 | Steel | K71040 | - | Forging |
![]() |